Aluminum 6061 vs. 7075: The Definitive Guide to Choosing Your Alloy
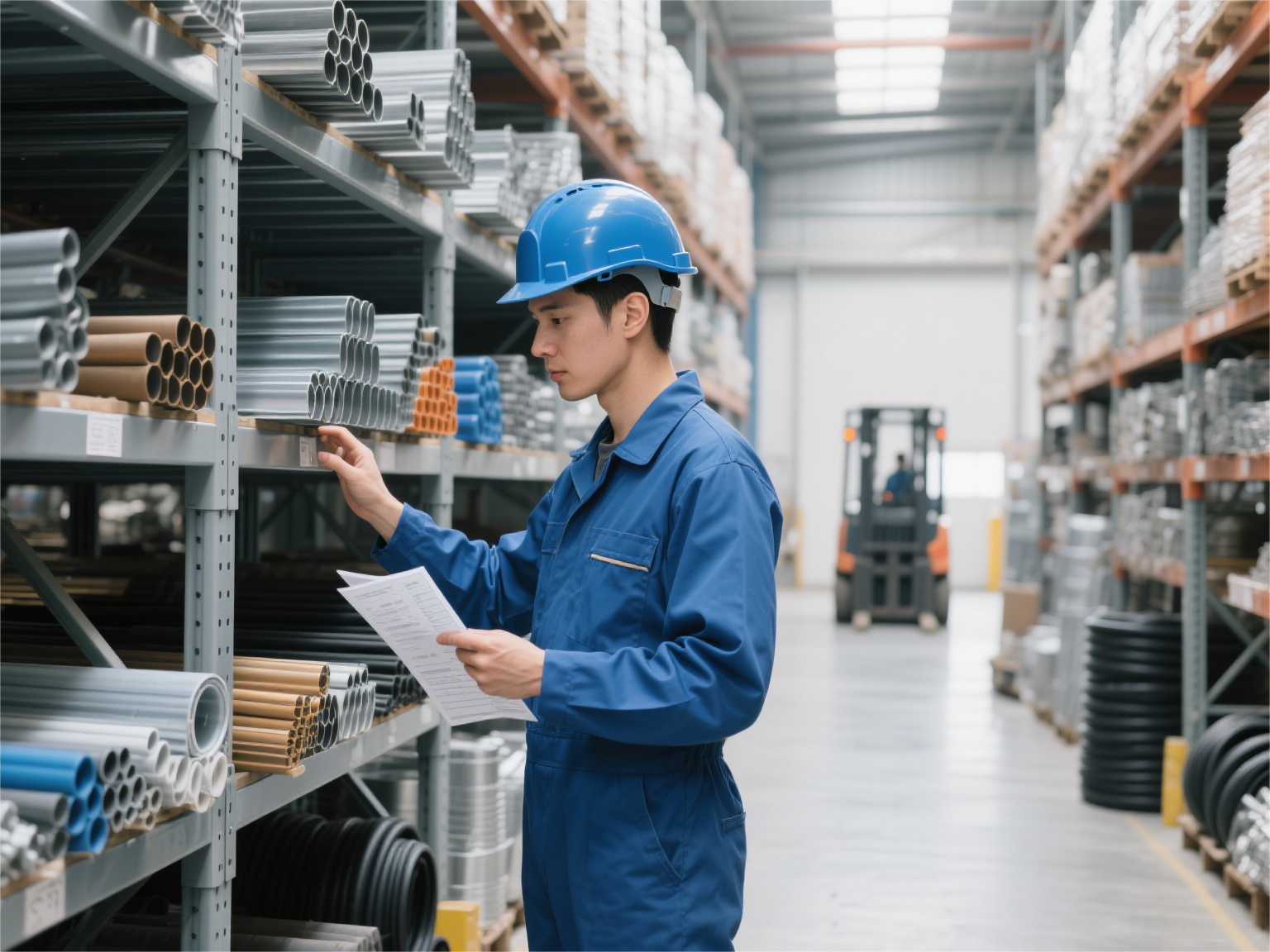
Composition and Metallurgy
Property | 6061 | 7075 |
---|---|---|
Primary Alloys | Magnesium (1.0%) + Silicon (0.6%) | Zinc (5.6%) + Magnesium (2.5%) + Copper (1.6%) |
Series | 6000 (heat-treatable) | 7000 (high-strength) |
Microstructure | Balanced α-Al matrix | Zn/Mg precipitates dominate |
Mechanical Properties Comparison
(T6 Temper Condition)
Parameter | 6061 | 7075 | Advantage |
---|---|---|---|
Tensile Strength | 45,000 psi | 83,000 psi | 7075: +84% |
Yield Strength | 40,000 psi | 73,000 psi | 7075: +82% |
Elongation | 12% | 11% | 6061: Better formability |
Fatigue Strength | 14,000 psi | 23,000 psi | 7075: +64% |
Hardness (Brinell) | 95 HB | 150 HB | 7075: +58% |
Performance Characteristics
✅ 6061 Advantages
-
Corrosion Resistance: Naturally forms protective oxide layer (ideal for marine/outdoor use)
-
Weldability: TIG/MIG friendly without cracking (unlike 7075)
-
Machinability: Softer material allows 30% faster feed rates
-
Cost: $5-7/kg vs. 7075’s $8-12/kg (40-70% savings)
🚀 7075 Advantages
-
Strength-to-Weight: 7075-T6 matches mild steel strength at 1/3 the weight
-
Impact Resistance: Absorbs 25% more energy before failure
-
Stiffness: 10.4×10⁶ psi modulus vs. 6061’s 10.0×10⁶ psi
Critical Limitations
Challenge | 6061 | 7075 |
---|---|---|
Stress Corrosion | Rare | Susceptible (requires cladding/anodizing) |
Cracking Risk | Low (post-weld) | High (avoid welding entirely) |
Anodizing Result | Consistent Type II/III | Often blotchy (needs specialized Type III) |
Industry Applications
6061 Dominates When:
-
Automotive frames (Ford F-150 bodies)
-
Bicycle frames (85% of mid-range bikes)
-
Marine components (corrosion resistance)
-
Structural profiles (extrusion-friendly)
7075 Excels When:
-
Aircraft structural parts (wing spars, Boeing 747 fittings)
-
High-stress tooling (drill jigs, injection molds)
-
Competition firearms (AR-15 receivers)
-
Racing components (F1 suspension arms)
Machining & Finishing Notes
Process | 6061 | 7075 |
---|---|---|
Optimal Feeds/Speeds | 800-1200 SFM (carbide) | 600-900 SFM (reduce chatter) |
Tool Wear | Low | High (use coated carbide) |
Surface Finish | Ra 0.8-3.2 μm achievable | Ra 1.6-6.3 μm (gummy chips) |
Post-Processing | Easy polishing/anodizing | Requires stress-relief before finishing |
Cost-Benefit Analysis
Example: Bracket Production (10,000 units)
Factor | 6061 Cost | 7075 Cost |
---|---|---|
Material | $12,000 | $21,000 (+75%) |
Machining Time | $8,000 | $11,000 (+38%) |
Tool Replacement | $1,500 | $4,500 (+200%) |
Total | $21,500 | $36,500 |
→ Use 7075 only if strength justifies 70% cost premium |
The Ultimate Selection Guide
Choose 6061 if:
-
Your design requires welding or bending
-
Corrosion resistance is critical
-
Budget constraints exist (prototypes/volume production)
-
Moderate strength suffices (automotive/consumer goods)
Choose 7075 if:
-
Strength-to-weight ratio is non-negotiable (aerospace/defense)
-
No welding is needed (use fasteners instead)
-
Fatigue resistance matters (moving components)
-
You accept additional finishing costs
“6061 is the ‘Swiss Army knife’ of aluminum; 7075 is a scalpel for surgical precision in high-stress applications.”
– Aerospace Materials Engineer
Verify your design requirements: For 80% of industrial applications, 6061 delivers optimal value. Reserve 7075 for mission-critical, strength-driven projects where failure is not an option.
-
Posted in
Aluminum Alloy, cnc machining, machining cost, precision machining, R&D, Raw Material Choose