Demystifying Surface Roughness Value: The Key to Functional Precision
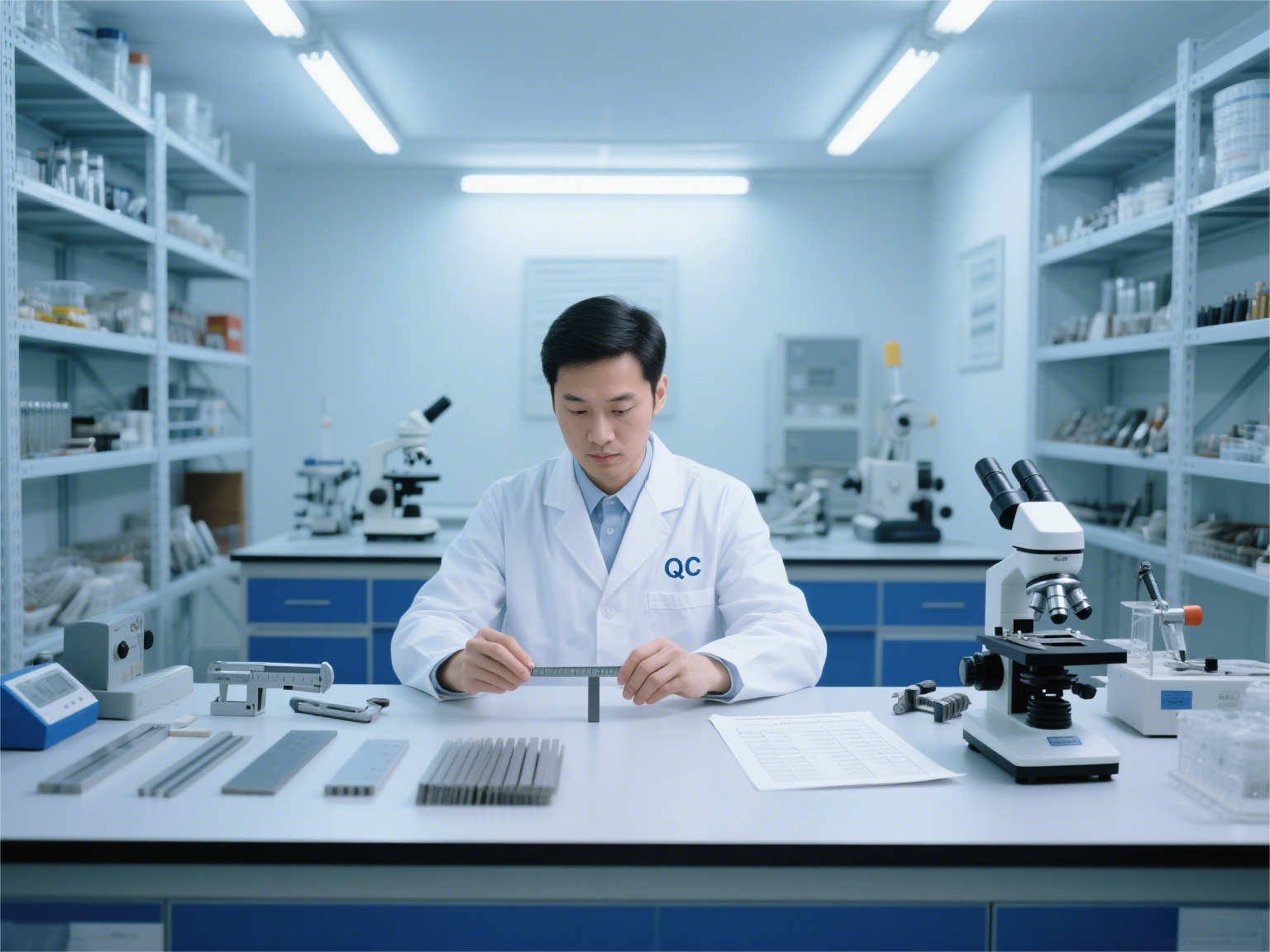
Core Measurement Parameters
Symbol | Name | What It Measures | Applications |
---|---|---|---|
Ra | Arithmetic Average | Average deviation from mean line | General-purpose tolerance (≈85% of specs) |
Rz | Average Maximum Height | Average distance between highest peak and deepest valley in sampling lengths | Critical interfaces (seals, bearings) |
Rt | Total Height | Maximum peak-to-valley height in entire scan | Safety-critical components (aerospace) |
Visual Comparison (Typical CNC Finishes):
-
Rough Machining: Ra 12.5 μm (500 μin) – Visible tool marks
-
Standard Finish: Ra 3.2 μm (125 μin) – Uniform tool paths
-
Smooth Finish: Ra 0.8 μm (32 μin) – Near-mirror appearance
How Surface Roughness is Measured
-
Contact Profilometers: Diamond-tipped stylus traces surface (accuracy down to 0.01 μm)
-
Optical Scanners: Laser/white light interferometry (non-contact, high-speed)
-
Comparison Samples: Visual/tactile match against standardized "roughness masters"
Controlling Roughness in CNC Machining
Adjust These Factors to Optimize Ra/Rz:
Factor | Effect on Roughness | Optimal Adjustment |
---|---|---|
Feed Rate | High feed = deeper grooves | ↓ Feed rate by 25-40% for finer finish |
Cutting Speed | Low speed = built-up edge | ↑ Speed within tool/material limits |
Tool Geometry | Worn tools increase Ra | Use sharp tools with large nose radius |
Stepover | Wide passes leave scallops | ≤50% tool diameter for finishing passes |
Vibration | Chatter marks ↑ roughness | ↑ Rigidity, ↓ overhang, use damped toolholders |
Industry-Specific Roughness Standards
-
Automotive: Ra 0.4–1.6 μm for cylinder walls
-
Medical Implants: Ra < 0.2 μm (prevents bacterial adhesion)
-
Hydraulic Seals: Rz ≤ 3.2 μm for leak-proof surfaces
-
Aerospace: Rt ≤ 5 μm on turbine blade roots
Practical Tips for Engineers
-
Specify Wisely: Demanding Ra 0.2 μm vs. 0.8 μm can triple machining costs
-
Note Direction: Lay pattern (parallel/perpendicular) affects function
-
Combine Processes: Use milling (Ra 1.6 μm) + vibratory finishing (Ra 0.4 μm)
-
Verify Critical Zones: Apply tight roughness only to functional surfaces
"Controlling roughness isn’t about achieving zeros – it’s about optimizing for function." – ASME B46.1 Committee
Surface roughness isn’t just a number – it’s the fingerprint of manufacturing quality. Understanding Ra/Rz/Rt enables smarter design, cost control, and reliability. Always consult your machinist early to balance specifications with practicality.
-
Posted in
cnc machining, machining cost, precision machining, Surface Roughness