Beyond Machining Marks: The Surface Finish Showdown for CNC Parts
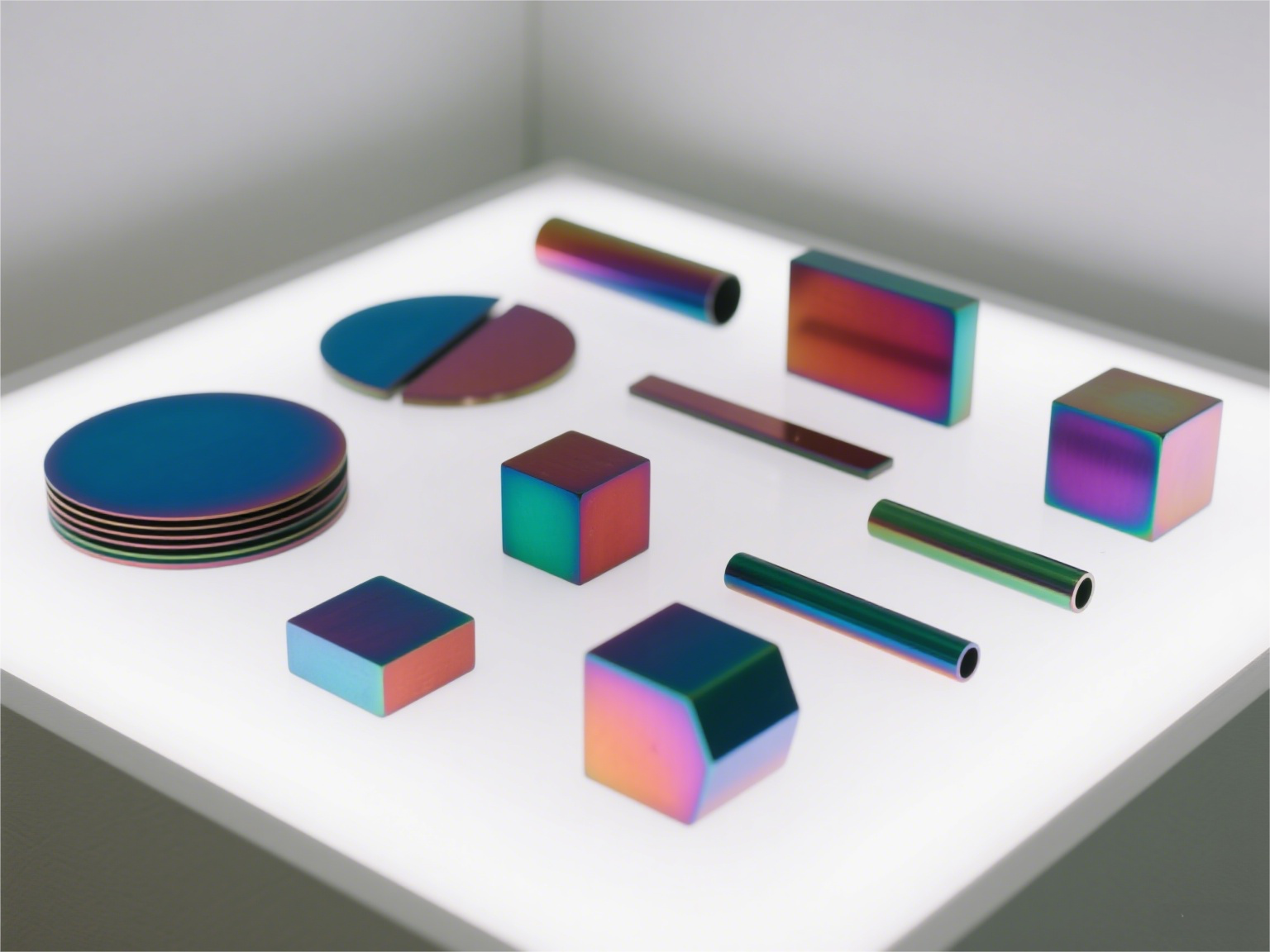
The Surface Treatment Spectrum: Processes & Mechanisms
1. As-Machined (No Post-Processing)
-
Why: Lowest cost; ideal for non-critical internal components
-
How: Directly after CNC milling/turning with standard tooling (no secondary steps)
-
Results:
-
Ra 0.8–3.2 μm (visible tool paths)
-
Vulnerable to oxidation; aluminum forms oxide layer in 48 hrs
-
Limited lifespan in dynamic loads
-
2. Bead Blasting
-
Why: Creates uniform matte texture; enhances coating adhesion
-
How: Propelling glass/Al₂O₃ grit (80–220 mesh) at 40–80 PSI
-
Results:
-
Ra 0.3–1.5 μm (depending on grit)
-
Increases surface area for anodizing adhesion by 40%
-
Hides minor machining defects
-
3. Standard Anodizing (Type II)
-
Why: Cost-effective corrosion protection for consumer goods
-
How: Electrochemical bath (15–20V) in sulfuric acid (180g/L, 18–22°C)
-
Results:
-
Thickness: 5–25 μm
-
Salt Spray Resistance: 500–1,000 hrs (vs. 48 hrs for bare Al)
-
Natural colors: Clear, black, gray
-
4. Hard Anodizing (Type III)
-
Why: Extreme wear resistance for aerospace/military applications
-
How: Low-temperature bath (0–5°C) at high voltage (40–100V)
-
Results:
-
Thickness: 50–100 μm
-
Hardness: 500–800 HV (comparable to tool steel)
-
Abrasion Loss: <0.1 mg/1,000 cycles (vs. 2.5 mg for untreated Al)
-
5. Color Anodizing
-
Why: Branding and aesthetic customization
-
How: Dye immersion after Type II anodizing; sealed in boiling water
-
Results:
-
Pantone-matching accuracy: ±5% ΔE
-
UV stability: 500+ hrs (for organic dyes)
-
Limitations: Dark colors fade faster; reds/oranges least stable
-
6. Black Oxide (for Steel)
-
Why: Low-glare corrosion barrier without dimensional change
-
How: Chemical conversion coating (140°C alkaline bath)
-
Results:
-
Thickness: 1–2 μm (adds zero part geometry change)
-
Corrosion Protection: 96 hrs salt spray (with oil sealant)
-
Emissivity: 0.85–0.95 (ideal for thermal components)
-
Performance Comparison: Data-Driven Selection
Table 1: Surface Treatment Performance Metrics (Aluminum 6061 Substrate)
Treatment | Ra (μm) | Hardness (HV) | Corrosion Resistance (hrs salt spray) | Adhesion (ASTM D3359) |
---|---|---|---|---|
As-Machined | 1.6–3.2 | 100 | 48 | N/A |
Bead Blasting | 0.3–1.5 | 100 | 48 | 5B (excellent) |
Standard Anodize | 0.4–0.8 | 200–300 | 500–1,000 | 4B (good) |
Hard Anodize | 0.8–2.0 | 500–800 | 2,000+ | 3B (fair) |
Black Oxide | 0.5–1.2 | N/A (steel only) | 96* | 4B (good) |
*With sealant |
Table 2: Cost & Lead Time Analysis (Per Batch)
Treatment | Cost Factor | Processing Time | Dimensional Impact |
---|---|---|---|
As-Machined | 1.0x | 0 min | None |
Bead Blasting | 1.3x | 10–30 min | ±0.01 mm |
Standard Anodize | 1.8x | 45–90 min | +0.01–0.03 mm |
Hard Anodize | 3.0x | 120–180 min | +0.05–0.10 mm |
Color Anodize | 2.2x | 90–120 min | +0.01–0.03 mm |
Black Oxide | 1.5x | 30–60 min | None |
The Strategic Selection Guide
When to Choose Which Finish
-
High-Wear Applications (gears, pistons):
-
Hard anodizing increases service life 5–8×
-
Avoid color anodizing (dyes reduce wear resistance)
-
-
Marine/Outdoor Environments:
-
Standard anodizing (clear) + 5% dichromate sealant
-
Bead blasting alone offers zero corrosion protection
-
-
Aesthetic-Critical Parts (consumer electronics):
-
#220 bead blast + color anodizing for uniform matte finish
-
Critical: Specify dye stability (inorganic > organic)
-
-
Precision Components (shafts, bearings):
-
Bead blasting (fine grit) to avoid dimensional shifts from anodizing
-
Black oxide for steel parts needing oil retention
-
Critical Design Considerations
-
Tolerances: Hard anodizing adds 50–100 μm – compensate in CAD
-
Material Limits:
-
Color anodizing: Best on aluminum/titanium (not steel)
-
Black oxide: Only for ferrous metals
-
-
Electrical Conductivity: Anodizing is non-conductive – mask contact points
Maximizing Value: Pro Tips from Industry
-
Sequential Processes: For high-end optics:
-
Machine → Glass bead blast (Ra 0.4 μm) → Hard anodize → PTFE sealant
-
-
Adhesion Boost: On blasted surfaces, anodizing bond strength improves 60%
-
Cost Savers:
-
Use hard anodizing only on wear surfaces (partial masking)
-
Specify Ra 1.6 μm instead of 0.8 μm where possible (cuts blasting time 35%)
-
"Surface finishing isn’t cosmetic – it’s functional engineering. A $5 treatment can save a $5,000 part."
– Aerospace QA Lead, Boeing Supplier Summit 2024
Conclusion: Match the Finish to the Function
CNC part performance hinges on surface science. While raw machining suits prototypes, production demands strategic post-processing:
-
Bead blasting for uniform matte aesthetics
-
Standard anodizing for corrosion-prone environments
-
Hard anodizing where wear determines product life
-
Color anodizing for branded consumer goods
-
Black oxide for dimensionally-sensitive steel components
Test first: Process coupons to validate adhesion, corrosion, and wear metrics before full production. Partner with finishers during design to optimize costs and lead times.
-
Posted in
cnc machining, precision machining, rapid prototyping, surface process