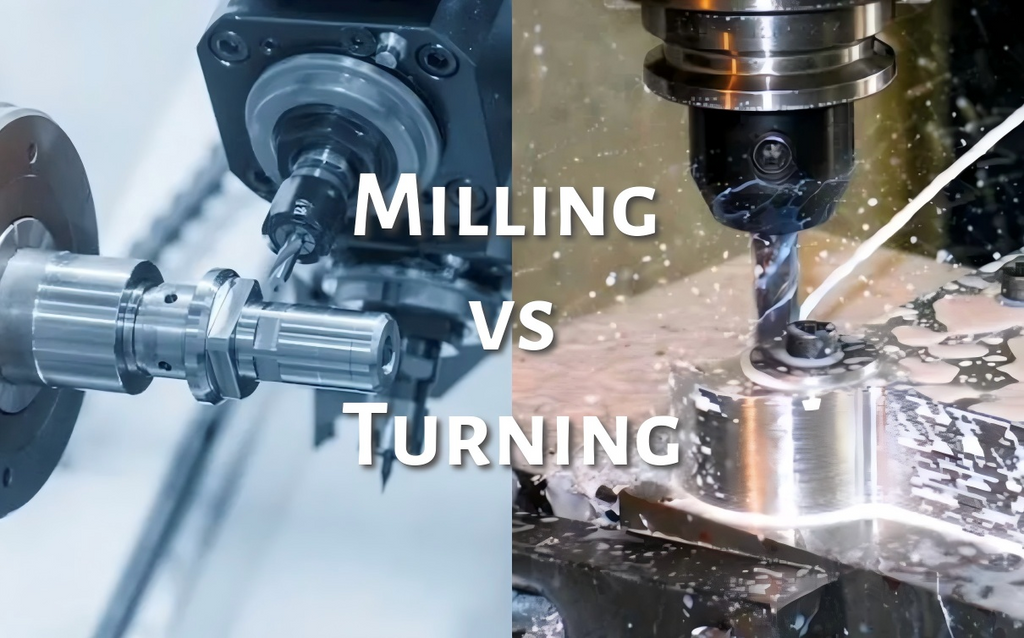
CNC Milling vs. Turning: The Ultimate Precision Manufacturing Key
Why Understanding the Difference Matters
Choosing between CNC milling and turning isn’t about finding a "better" process—it’s about matching the technology to your part’s geometry, material, and functional requirements. Milling excels at complex 3D contours and asymmetric features, while turning dominates for cylindrical symmetry and rotational precision. Misapplying these methods leads to:
-
50–70% higher machining costs from inefficient material removal
-
Dimensional inaccuracies due to improper toolpath forces
-
Extended lead times from unnecessary setups or rework
Understanding their core differences unlocks faster production, tighter tolerances, and 20–30% cost savings.
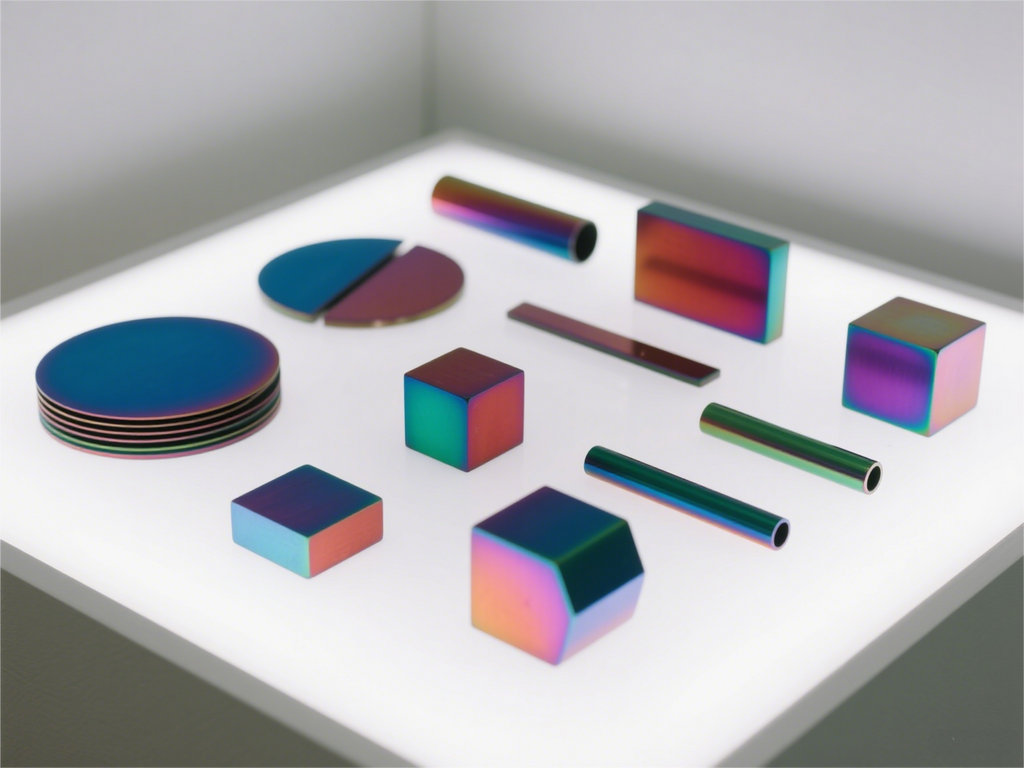
Beyond Machining Marks: The Surface Finish Showdown for CNC Parts
Why Surface Treatment Matters More Than You Think
CNC-machined parts rarely perform optimally straight off the machine. Raw surfaces retain visible tool marks (Ra 1.6–6.3 μm), creating stress concentration points that reduce fatigue life by 15–30% . Post-processing eliminates these flaws while adding critical functionality: corrosion resistance, wear protection, aesthetic appeal, or dimensional stability. Selecting the wrong finish risks part failure, unnecessary costs, or rejected designs.
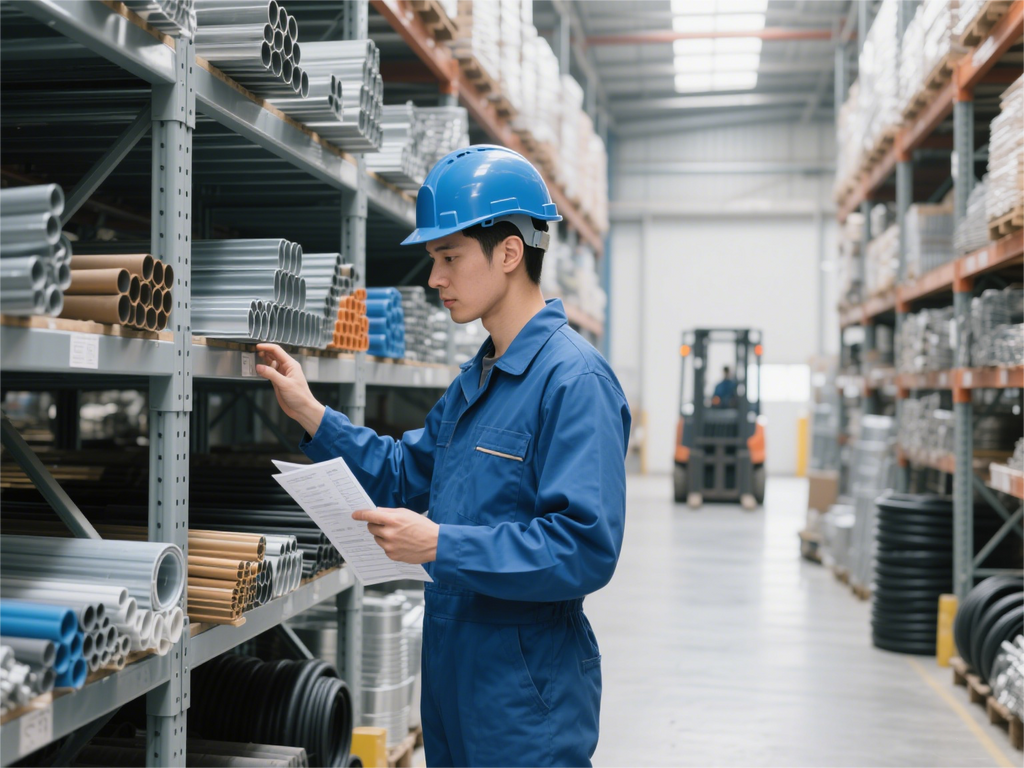
Aluminum 6061 vs. 7075: The Definitive Guide to Choosing Your Alloy
Introduction: The Critical Crossroads
In precision engineering, selecting the right aluminum alloy can mean the difference between optimal performance and catastrophic failure. 6061 and 7075 – two of the most widely used alloys – sit at opposite ends of the aluminum spectrum. While 6061 offers versatility and economy, 7075 delivers aerospace-grade strength. Yet misapplying either can lead to costly redesigns, premature failures, or bloated budgets.
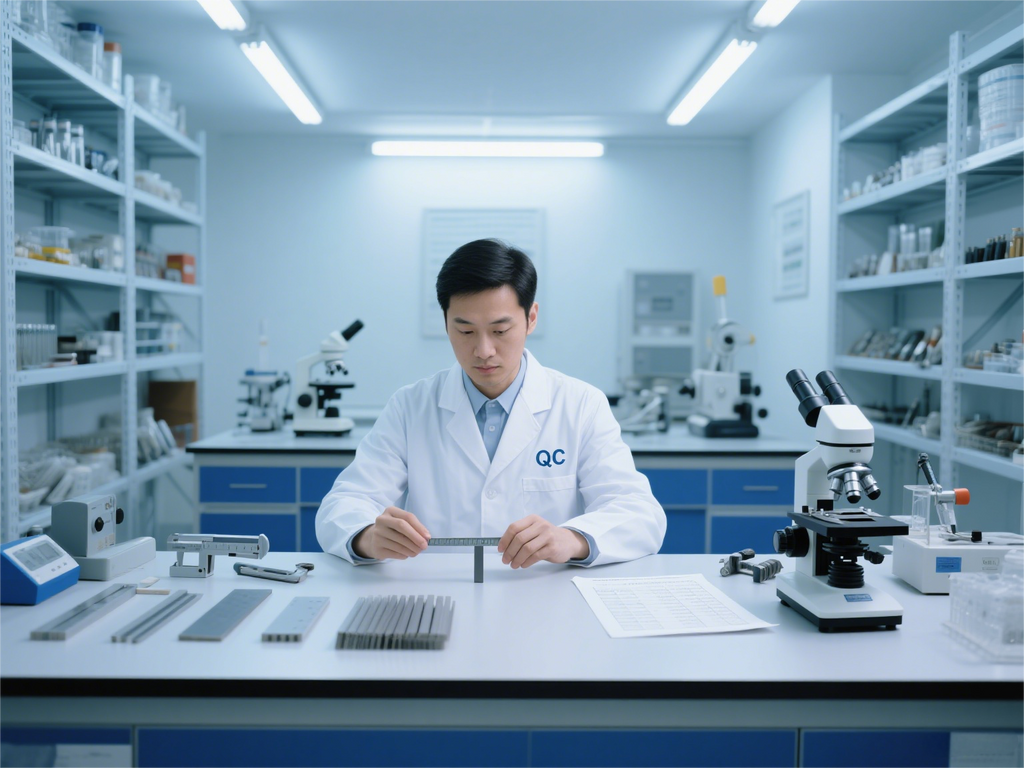
Demystifying Surface Roughness Value: The Key to Functional Precision
Why Surface Roughness Matters
Surface roughness quantifies microscopic peaks and valleys on machined parts. It directly impacts:
-
Functional Performance: Friction, wear, sealing, lubrication retention
-
Aesthetics: Visual appearance and light reflection
-
Manufacturing Cost: Finer finishes require additional operations (grinding, polishing)

Smart Strategies to Optimize CNC Machining Costs Without Sacrificing Quality
Why CNC Machining Costs Add Up Quickly
CNC machining is renowned for its precision, consistency, and flexibility, but these advantages come at a price. The primary cost drivers include machining time (the largest expense, often exceeding material or setup costs), material expenses, setup and CAM, and specialized tooling or tolerances. Complex geometries, deep cavities, thin walls, or non-standard features exponentially increase production time and resource use. For instance, machining a deep pocket might require incremental tool passes with specialized cutters, while strict tolerances demand slower speeds, advanced equipment, and rigorous inspections
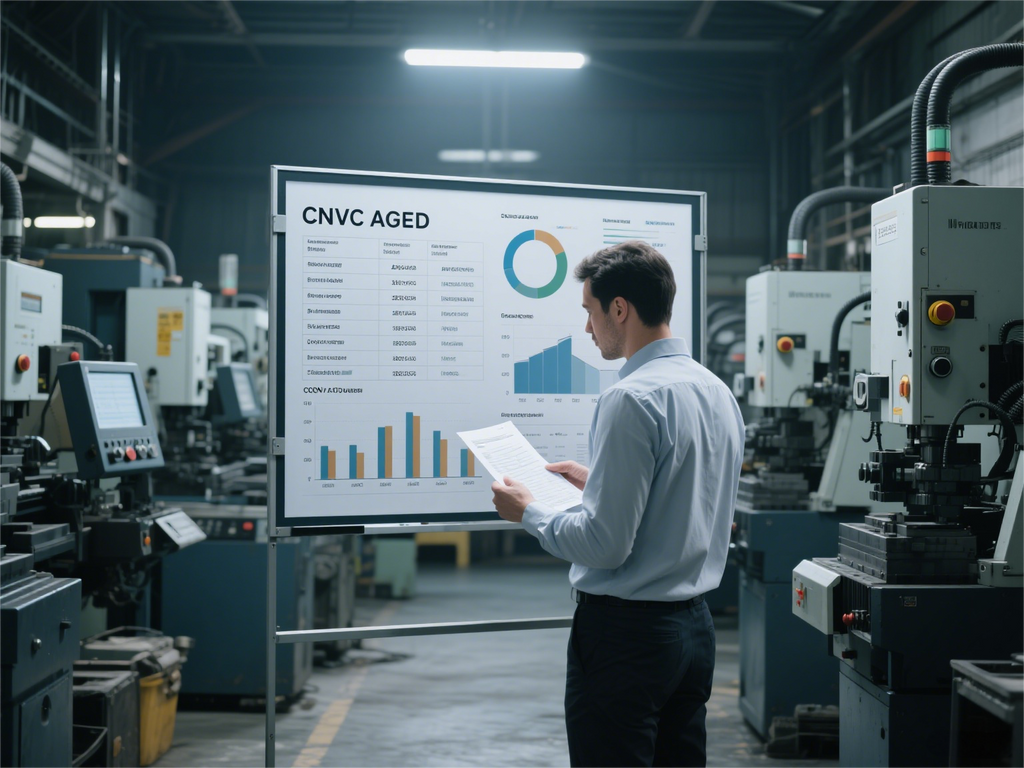
How is the Cost of CNC Machining Determined?
CNC machining costs are primarily driven by material selection (40-60%), machine time (amplified by 5-axis complexity), and geometric tolerances (±0.025mm can increase costs 150%). Hidden expenses include tool wear (e.g., $0.38/min for titanium) and post-processing. To optimize:
-
Partner with factory demonstrating ISO-certified 5-axis precision (±5μm)
-
Demand operation-level cost breakdowns
-
Prioritize vendors offering scientific DFM feedback within 24h
True cost efficiency comes from technical collaboration, not price negotiation – strategic partnerships reduce TCO by 18-32% through process innovation.
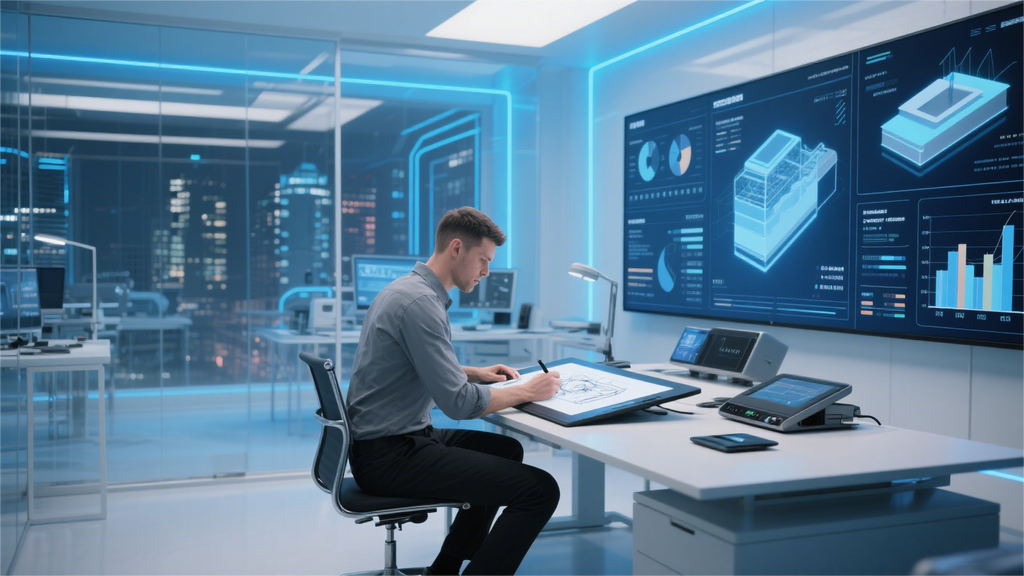
CNC Machining in Rapid Prototyping: Integrated Workflow from Digital Design to Precision Machining
Core Value: Enables deterministic transformation of CAD data into dimensionally compliant prototypes, accelerating product validation cycles across automotive, aerospace, medical, and consumer electronics sectors.