CNC Milling vs. Turning: The Ultimate Precision Manufacturing Key
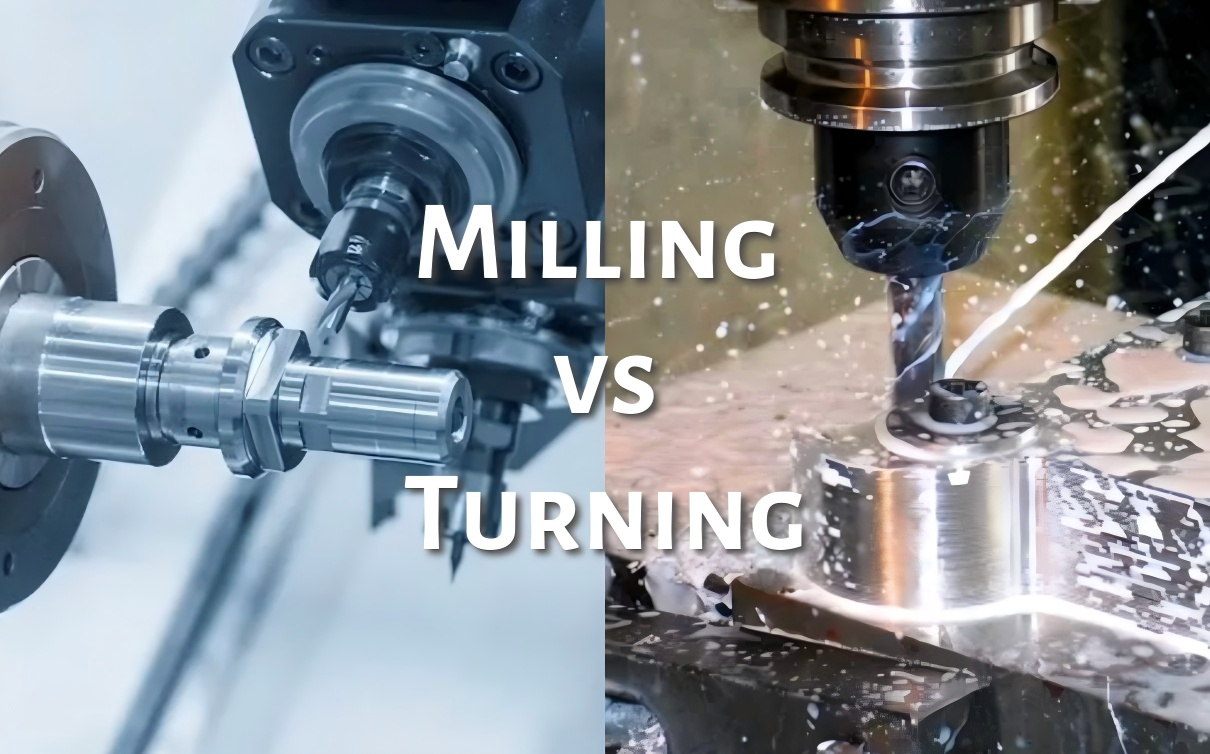
The Core Divide: How Milling and Turning Work
CNC Turning (The Rotation Master)
-
Why it works: Ideal for parts with rotational symmetry (shafts, bushings, cones). The rotating workpiece meets a fixed cutting tool, enabling high concentricity (±0.005 mm).
-
How it’s done:
-
The workpiece spins on a chuck (up to 5,000 RPM).
-
Tools move linearly to cut diameters, faces, or threads.
-
Live-tooling attachments add drilling/milling capabilities for hybrid operations.
-
-
Results: Mirror finishes (Ra 0.4–1.6 μm) on cylinders with cycle times 30–50% faster than milling for axisymmetric parts.
CNC Milling (The Multiaxis Sculptor)
-
Why it works: Best for complex geometries (pockets, planes, 3D contours). Rotating tools (end mills, face mills) remove material as the workpiece feeds.
-
How it’s done:
-
3–5 axes of tool motion (horizontal/vertical/rotational).
-
Tools like ball-nose end mills machine organic curves.
-
Adaptive toolpaths optimize material removal rates.
-
-
Results: Capable of ±0.025 mm tolerances on intricate molds, aerospace brackets, and non-rotational parts.
Table 1: Functional Comparison of Milling vs. Turning
Aspect | CNC Milling | CNC Turning |
---|---|---|
Primary Function | Flat/curved surfaces, pockets | Cylindrical shapes, tapers |
Part Movement | Static or linear feed | Rotational (up to 5,000 RPM) |
Tool Movement | Multi-axis (X/Y/Z + rotational) | Linear (X/Z-axis) |
Surface Finish | Ra 0.8–3.2 μm (matte/textured) | Ra 0.4–1.6 μm (smooth/polished) |
Complexity | High (organic shapes, thin walls) | Medium (facing, grooving, threading) |
Cost Analysis: Breaking Down the Economics
Machine Investment
-
Entry-level turning: Manual lathes start at $15K (vs. $50K+ for 3-axis mills).
-
High-end hybrid: 5-axis mill-turn centers exceed $500K but eliminate secondary ops.
Operational Efficiency
-
Turning wins for cylinders: 30% faster cycle times vs. milling similar geometries.
-
Milling wins for complexity: Single-setup machining reduces handling costs by 40%.
*Table 2: Cost-Per-Part Comparison (Aluminum 6061)*
Process | Setup Cost | Cycle Time (min) | Tooling Cost | Ideal Batch Size |
---|---|---|---|---|
CNC Turning | $120–$300 | 5–15 | Low ($20–$50) | 100–10,000 units |
CNC Milling | $250–$800 | 20–60 | High ($100–$500) | 1–1,000 units |
Mill-Turn | $500–$1,500 | 10–30 | Medium ($50–$200) | 50–5,000 units |
Key Insight: For prototypes or complex low-volume parts, milling provides flexibility. For high-volume rotational parts, turning cuts costs by 25–40%.
Industry Applications: Where Each Shines
Turning Dominates in:
-
Automotive: Engine pistons, transmission shafts (1 million+ units/year).
-
Medical: Bone screws, hip stems (Ra < 0.8 μm critical for implants).
-
Energy: Valve bodies, hydraulic fittings (cyclic symmetry required).
Milling Excels in:
-
Aerospace: Turbine blades, wing ribs (5-axis contouring).
-
Consumer Electronics: Phone chassis, heat sinks (thin-wall machining).
-
Tooling: Injection molds, die-casting cavities (hardened steel > 45 HRC).
Emerging Hybrid Solution: Mill-turn centers (e.g., Mazak Integrex) combine both technologies. The market is projected to reach $8.4B by 2030, driven by aerospace/medical demand for "done-in-one" machining.
The Future: AI and Hybridization
Smart Optimization
-
Machine learning algorithms adjust feeds/speeds in real-time:
-
Reduce tool wear by 20% in turning.
-
Predict chatter in milling, boosting surface quality.
-
-
Prime Turning™ (Sandvik): Novel toolpaths increase turning feed rates by 300% and extend tool life 5×.
CAM Software Advancements
Tools like Mastercam and Fusion 360 unify milling/turning programming:
-
Auto-feature recognition slashes programming time by 50%.
-
Simulation prevents collisions in complex mill-turn operations.
Decision Guide: 5 Questions to Choose Right
-
Part geometry: Rotational symmetry? → Turning. Complex 3D contours? → Milling.
-
Volume: >500 units? → Turning or mill-turn. <100? → Milling.
-
Material: Hard metals (Ti, tool steel)? → Milling for tool rigidity. Soft alloys (Al, brass)? → Turning for speed.
-
Tolerances: < ±0.025 mm? → Mill-turn for single-setup accuracy.
-
Budget: Under $100K? → Standalone lathe or 3-axis mill. Over $300K? → Hybrid mill-turn.
"Forcing a square peg into a round hole costs more than buying the right machine. Turning and milling are complementary – not competing – technologies."
– Manufacturing Engineer, Boeing Supplier Summit 2025
The Verdict: Synergy Over Superiority
No process is universally "better." High-volume cylindrical components benefit from turning’s speed and surface finish. Complex, low-volume parts leverage milling’s geometric freedom. For mission-critical applications like aerospace turbines or medical implants, mill-turn centers deliver the best of both worlds:
-
30–50% faster than separate operations
-
20% lower costs via reduced handling
-
True position accuracy under 0.01 mm.
Test both: Run prototyping batches using milling and turning to compare quality, lead time, and cost. Partner with CAM experts to optimize your strategy – the right choice saves thousands per project. For cutting parameters or machine selection datasets, request our benchmark reports.
-
Posted in
cnc machining, Milling, precision machining, rapid prototyping, Turning